Onsemi: Haute intégration et flexibilité maximale du pilote de commande moteur
Contrairement au moteur à courant continu à balais classique, qui est mécaniquement auto-commuté, la commande de moteur triphasé à courant continu sans balais (BLDC) à aimant permanent nécessite un circuit de commutation électronique.
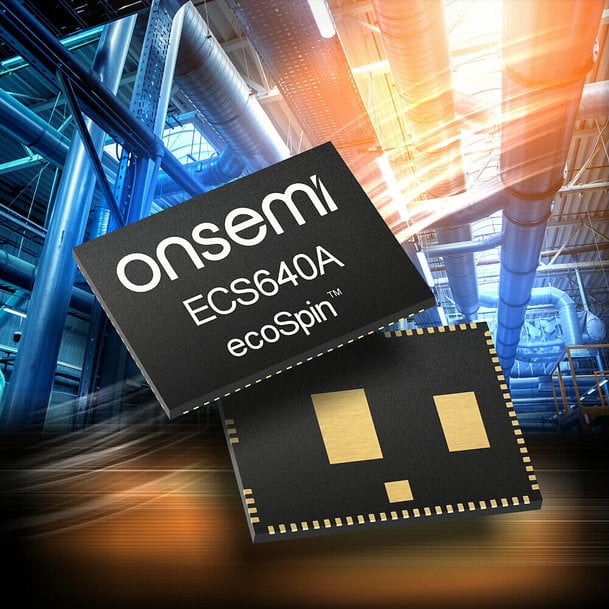
Par Joe Howell, Ingénieur Système Senior, onsemi
Dans cet article, nous rappelons brièvement le principe de fonctionnement du moteur BLDC, avant d'examiner les caractéristiques, les avantages et les inconvénients de deux des méthodes de commutation les plus utilisées en termes de complexité, d'ondulations de couple, et de rendement. Nous examinons ensuite une nouvelle approche innovante de la commutation BLDC, et discutons des caractéristiques et des avantages d'un nouveau circuit intégré (CI) de commande moteur onsemi, capable de mettre en œuvre l'une des trois méthodes de commutation.
Architecture du moteur BLDC
Le moteur BLDC est un moteur électrique rotatif qui se compose d'enroulements d'induits triphasés pour le stator, et d'aimants permanents pour le rotor. La structure mécanique du moteur BLDC est l'inverse de celle du moteur conventionnel à courant continu à aimants permanents et à balais, le rotor contenant les aimants permanents. En revanche, les enroulements du moteur sont montés sur le stator. Toutefois, comme son nom l'indique, le moteur BLDC est dépourvu de balais nécessitant un entretien ou un remplacement périodique, ce qui le rend moins sensible à l'usure. Les aimants permanents du rotor de moteur BLDC assurent un champ magnétique constant qui permet d'obtenir un moteur à haut rendement, à couple élevé et à faible moment d'inertie.
La fiabilité inhérente et la capacité d'entraînement à vitesse variable du moteur BLDC le rendent populaire pour de nombreuses applications, notamment les produits electroménagers, les systèmes de chauffage, ventilation et climatisation (CVC), l'automobile, et les machines industrielles, y compris la robotique. Le circuit de commutation pour moteur BLDC triphasé est généralement mis en œuvre avec des composants discrets ou avec un MCU et un module de puissance intégré. Une conception à base de composants discrets nécessite une grande expertise en matière de conception pour l'architecture et le dépannage, ainsi que du temps pour la mise en œuvre. Utiliser un circuit intégré de commande moteur dédié associé à un étage de puissance discret est devenu une approche plus populaire, car aucun ou peu de circuits supplémentaires ne sont nécessaires, et de nombreux fabricants fournissent un logiciel dédié avec leur produit, ce qui simplifie considérablement la configuration et le débogage.
Une solution 100% discrète peut souvent minimiser le coût des composants de la solution. Cependant, une solution plus intégrée réduit le coût global du système grâce à la réduction de la surface occupée sur le circuit imprimé et du nombre d’étapes de fabrication - ce qui permet de réduire la nomenclature et les coûts d'inventaire, et de favoriser la réutilisation de variantes de la solution dans de nouvelles conceptions - tout en augmentant la fiabilité globale de la solution. Désormais, un CI de contrôle dédié à étage de puissance discret est également disponible chez onsemi.
Commande de moteur BLDC
Contrairement à celui d’un moteur à courant continu à balais typique, le système de commande d'un moteur BLDC est connu sous le nom d’inverseur onduleur. Il se compose d'un étage de puissance pour piloter le moteur, d'amplificateurs de détection pour mesurer les signaux de force électro-motrice permettant le fonctionnement sans capteur, d'un encodeur ou de capteurs à effet Hall pour le fonctionnement avec capteur, et d'un contrôleur à base de microcontrôleur (MCU). Le contrôleur convertit les informations de retour de vitesse et de position en signaux PWM permettant la commande dynamique du moteur. Le coût et la complexité accrus d'un système à base d’inverseur onduleur sont compensés par de nombreux avantages : fiabilité et efficacité énergétique accrues, réduction du bruit, plage de fonctionnement plus large et excellente régulation de vitesse et de couple. La mise en œuvre d'un onduleur BLDC nécessite une expertise supplémentaire en matière de conception électronique, d’implantation et de programmation de micrologiciel, ainsi qu'un accès aux outils et ressources nécessaires pour accomplir ces tâches.
Deux algorithmes de commutation largement utilisés pour la commande de moteur BLDC sont la commande trapézoïdale et la commande à flux orienté (FOC), également connue sous le nom de commande vectorielle. La commutation trapézoïdale est la plus simple, mais c'est la moins efficace et la plus bruyante. Le FOC est plus complexe à mettre en œuvre mais elle est généralement plus silencieuse et plus efficiente. Les deux méthodes peuvent être avec ou sans capteur.
Figure 1 Schéma d’un moteur BLDC montrant l'emplacement des capteurs à effet Hall (https://www.onsemi.com/pub/collateral/tnd6041-d.pdf)
Commutation trapézoïdale
La commutation trapézoïdale utilise deux dispositifs de commutation de puissance sur chaque phase du moteur, qui suivent une séquence « marche-arrêt » prédéterminée. Cette méthode est populaire du fait de la simplicité de l'algorithme de commande et de la possibilité de l'implémenter sur des MCU rudimentaires. La commande trapézoïdale est très efficace pour contrôler la vitesse du moteur, mais c'est la méthode la moins efficace au niveau énergétique. Elle souffre aussi de fortes ondulations de couple pendant la commutation, en particulier à basse vitesse, et reste donc surtout populaire pour les applications bas de gamme nécessitant un fonctionnement simple en boucle fermée. Les ondulations de couple importantes sont dues aux non-linéarités, car seuls deux des trois enroulements du moteur transportent du courant à un moment donné. Par conséquent, les non-linéarités génèrent du bruit et des vibrations, et le contrôleur de courant doit être suffisamment lent pour ne pas réagir aux transitoires dues au transfert de courant passant d'une phase à l'autre, ce qui limite les performances globales. Une méthode de commutation à 180° permet de générer un couple élevé avec une commutation trapézoïdale, mais une commutation à 120° minimise les ondulations de couple. La séquence de commutation est déterminée pour conduire deux phases consécutives du moteur (avec un intervalle de 60°) quand le moteur tourne.
Figure 2 Signaux de commande trapézoïdale en 6 étapes
(https://www.onsemi.com/pub/collateral/tnd6041-d.pdf)
Commande à flux orienté (FOC)
La FOC est une méthode de commutation plus complexe, avec des exigences de traitement plus élevées, ce qui la réserve davantage aux applications haut de gamme. Les avantages de la FOC par rapport à la commande trapézoïdale sont notamment un positionnement précis, une vitesse maximum plus élevée, des ondulations de couple réduites et un niveau de bruit plus faible, ainsi qu'un meilleur rendement énergétique. Avec la FOC, le moteur est commuté sans capteur en calculant les vecteurs de tension et de courant sur la base du retour de courant moteur, mais il peut aussi utiliser des capteurs à effet Hall si l'application l'exige.
La FOC maintient un rendement élevé sur une large plage de fonctionnement, tout en permettant une régulation dynamique précise de la vitesse et du couple. Dans le cas de la FOC, les trois courants du stator sont représentés sous forme d’un vecteur résultant des composantes orthogonales du couple et du flux magnétique. Les transformations mathématiques de Clarke et Park convertissent les formes d'onde de courant et de tension alternatifs variables en fonction du temps en valeurs continues, ce qui simplifie considérablement les exigences de traitement en aval. Le principal inconvénient de la commande FOC est la puissance de traitement accrue nécessaire, qui peut nécessiter un MCU plus puissant.
Commande directe de couple et de flux
Bien que le DTC et le DTFC existent depuis un certain temps, une nouvelle approche de la commutation BLDC sans capteur a été développée par Theta Power Solutions, Intl (TPSI) pour commander directement le couple et le flux. Bien que le concept de DTFC ne soit pas nouveau, TPSI a mis au point une méthode unique et plus efficace pour fournir aux moteurs BLDC un affaiblissement du flux permettant une vitesse de rotation plus élevée. Il est idéal pour les algorithmes de freinage, qui doivent assurer une décélération contrôlée avec des charges inertielles élevées. Il utilise un bus de données à haut débit qui achemine les informations de retour moteur en temps réel pour fournir un couple maximum par ampère (MTPA) de courant de commande. Il assure un rendement élevé du moteur dans toutes les conditions de charge (même en saturation), et dispose d'une compensation thermique pour les moteurs fonctionnant en permanence ou à des températures extrêmes. Pour les applications nécessitant un couple précis à des vitesses très basses, l'implémentation de TPSI constitue une excellente solution sans capteur, qui permet à l'utilisateur de réduire le coût du système puisqu’aucun capteur n’est nécessaire.
Parmi les avantages de l’implantation de TPSI par rapport au DTC traditionnel (et au FOC), on peut citer, entre autres :
- Démarrage en boucle fermée avec appel de courant très faible
- Stabilité supérieure sur des plages de vitesse étendues
- Fonctionnement sans capteur, de par sa nature même
- La télémétrie rapide permet d'utiliser le moteur comme capteur
- Couple maximal par Ampère
- Bruit est réduit au minimum
- Excellente performance à basse vitesse (~5 Hz) sans capteurs
- Meilleure régulation du couple dans sa catégorie sur toute la plage de vitesse
- Interface utilisateur simplifiant la mise en route rapide du moteur
Le DTFC de TPSI nécessite une puissance de traitement supplémentaire pour être mis en œuvre. L'ECS640A est une première industrielle avec cette technique de contrôle avancée mise en œuvre sur un MCU de classe Arm® Cortex®-M0+.
Choix de commande 3-en-1
La famille ecoSpin™ de contrôleurs de moteur configurables d’onsemi permet de choisir parmi les trois méthodes de commande évoquées précédemment. L'ECS640A, premier dispositif de cette famille, est une solution de type système en boîtier (SiP). Il intègre un microcontrôleur Arm® Cortex®-M0+, trois amplificateurs de détection, un amplificateur de référence, trois diodes d'amorçage et un driver de grille haute tension conçu pour un fonctionnement à haute tension et vitesse élevée, le tout dans un même boîtier QFN de 10 x 13 mm. Il est capable de piloter des MOSFET et des IGBT fonctionnant jusqu'à 600 V (FAN73896), et dispose de six sorties driver de grille permettant d’absorber ou de fournir un courant de grille de 350 mA à 650 mA (typique) à des dispositifs de puissance externes. Le dispositif composant dispose d’entrées GPIO pour capteurs à effet Hall afin de pouvoir prendre en charge le fonctionnement en mode détection si nécessaire, et il est aussi doté de trois broches source indépendantes côté bas, qui permettent d'effectuer des mesures de shunt simples ou multiples.
Son faible encombrement et son niveau d’intégration en font un candidat parfait pour une utilisation avec des dispositifs composants de puissance discrets permettant une évolutivité maximum. Il est fourni avec un kit de développement logiciel (SDK), composé d'un chargeur flash, de fichiers système et d’amorçage du dispositif, de drivers de périphériques (style CMSIS-Driver) et d'un exemple de code pour la démonstration de périphériques. onsemi a également collaboré avec Theta Power Solutions, Inc. pour fournir un micrologiciel DTFC disponible pour l'ECS640A. Cela permet d'optimiser les performances du moteur avec le processeur Arm Cortex-M0+ sans avoir à gérer la commutation avec une solution MCU plus puissante et plus coûteuse.
L'interface utilisateur graphique facile à utiliser simplifie le développement du code et réduit les délais de commercialisation. Les utilisateurs apprécieront la solution intégrée, qui génère automatiquement les paramètres pour le moteur spécifique utilisé, ce qui permet de configurer le système et de le faire fonctionner rapidement, plutôt que de se perdre dans les détails de rotation du moteur.
Flexibilité et intégration
Les moteurs BLDC sont de plus en plus populaires dans de nombreuses applications, mais nécessitent une commutation appropriée pour fournir tous leurs avantages. Lors de la sélection d'un CI de commande de moteur BLDC, il est logique de choisir celui qui offre le plus grand nombre d'options de commutation avec une intégration élevée. Le contrôleur de moteur ECS640A onsemi offre à la fois flexibilité et facilité d'utilisation pour les applications avec ou sans capteur.
www.onsemi.com