www.industrieweb.fr
10
'19
Written on Modified on
La première pièce de sécurité imprimée en 3D approuvée par le secteur ferroviaire
Les économies permises par la fabrication additive en terme de réduction des délais de fabrication et des stocks de pièces détachées, constituent un argument de poids pour les compagnies aéronautiques ou ferroviaires.
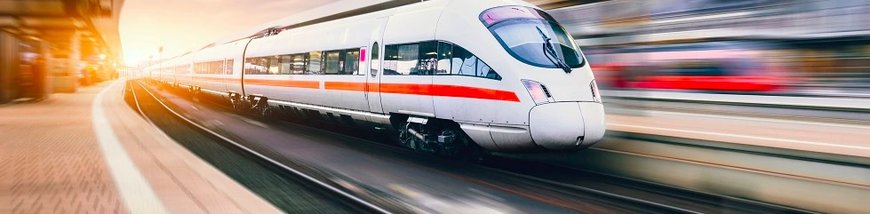
Si jusqu’alors, du fait notamment du long processus de qualification, ce sont essentiellement des pièces d’intérieurs (accoudoirs, appuies-tête, cadres d’écran…), qui étaient produites de manière additive, les cas d’applications pour des pièces plus critiques commencent à émerger. Ce jeudi, Mobility goes Additive, l’un des plus importants réseaux d’entreprises, d’institutions et d’instituts de recherche qui travaillent sur les solutions de fabrication additive, a annoncé l’approbation du premier composant de fabrication additive destiné à la sécurité du secteur ferroviaire. La pièce en question est un bras de liaison de frein mis en service sur un métro de la compagnie allemande Hamburger Hochbahn AG. Interrogée par Primante 3D quant au processus d’impression, Mobility Goes Additive explique que la pièce a été imprimée par fusion sur lit de poudre sur un inox de type 1.4404. L’impression a duré exactement 3 jours, 21 heures et 35 minutes, auquel il a fallu ajouter 7 heures de post-traitement.
Dirigé par Siemens Mobility avec la participation de ses membres Deutsche Bahn et des installations Fraunhofer IAPT et IGCV, le groupe de travail Approbation du réseau MGA avait commencé le développement de la pièce en 2017. C’est le TÜV SÜD, l’autorité de surveillance technique de Hambourg qui lui a accordé un agrément opérationnel, ce qui a conduit à sa mise en service en août 2019.
« En un peu moins de deux ans, son objectif d’obtenir une première homologation pour l’utilisation opérationnelle d’un composant de fabrication additif, hautement sollicité et important pour la sécurité a été atteint. » A déclaré Mobility goes Additive. « À la suite d’un concept d’approbation développé conjointement, l’adéquation du composant imprimé 3d pour la vie réelle a été démontrée avec succès. Les procédures d’assurance qualité nécessaires, les tests approfondis et les documentations correspondantes ont finalement été évalués par TÜV Süd Rail GmbH et approuvés. »
Qualifier des pièces imprimées en 3D pour répondre à des exigences de sécurité strictes.
BOStrab, qui est l’organisme en charge des réglementations fédérales allemandes relatives à la construction et à l’exploitation de systèmes de train léger sur rail, et qui a également participé à l’approbation de la pièce imprimée en 3D, sera en charge d’établir une norme pour les approbations futures dans le but d’augmenter l’application des composants imprimés en 3D et des pièces de rechange dans le secteur ferroviaire.
C’est la compagnie allemande Deutsche Bahn AG, deuxième opérateur ferroviaire en Europe qui a créé le réseau « Mobility goes Additive » en septembre 2016. Sa création avait pour but de faciliter les interactions entre entreprises, institutions et chercheurs dans le domaine des solutions additives pour le secteur de la mobilité et de la logistique. À l’instar de l’industrie aérospatiale, l’un des principaux défis auxquels Deutsche Bahn est confrontée, réside dans la qualification des pièces imprimées en 3D pour répondre à des exigences de sécurité strictes.
Pour établir un catalogue numérique de pièces de rechange, le réseau Mobility Goes Additive collabore avec le développeur de logiciels d’impression 3D 3YOURMIND. L’utilisation de son logiciel AMPI (Additive Manufacturing Part Identifier) permet de sélectionner automatiquement les pièces les plus appropriées pour l’impression 3D. Sur la base des résultats, les ingénieurs peuvent ensuite déterminer les applications d’impression 3D les plus efficaces pour passer ensuite à la production. En début d’année DB avait déjà imprimé près de 15 000 pièces de rechange et autres produits ; réalisant ainsi des économies substantielles tout en réduisant les temps d’arrêt des véhicules.
http://www.primante3d.com