www.industrieweb.fr
07
'19
Written on Modified on
Hager Group Optimise ses Applications d’Outillage et de Production avec la Fabrication Additive de Stratasys
Cela inclut la production de pièces d’outillage, remplaçant le métal utilisé précédemment.
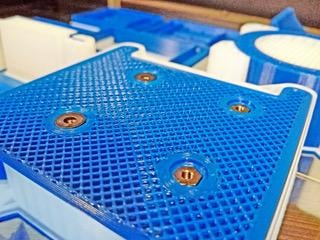
Alexandre Callegher, Développeur Mécanique, Département R&D, Hager Group.
Résumé
Hager Group est un des principaux fournisseurs leaders en matière de solutions et de services pour les installations électriques dans les bâtiments résidentiels, tertiaires et industriels. L’entreprise a été fondée en 1955 et reste aujourd’hui une entreprise indépendante, dirigée par les membres de la famille Hager, avec 11 400 employés. Les solutions sont produites dans 23 sites dans le monde, et notamment sur le site de Saverne en France.
Dans le but de rester innovant tout en réduisant les délais et coûts de production, l’équipe R&D de Saverne cherchait à intégrer des solutions de fabrication additive à niveau industriel à ses procédés de conception et de production. Après avoir investi dans la technologie 3D PolyJet™ de Stratasys, l’entreprise a acquis un système de production Fortus 380mc™ de Stratasys, et utilise désormais la technologie FDM pour la création d’outillage de pointe.
Avantages et valeurs
Hager Group a vu un retour sur investissement dans les premiers 18 mois d’utilisation du système de production Fortus 380mc de Stratasys Des pièces d’outillage personnalisées et en faible volume imprimées en 3D sur place dans les 24 heures de la requête initiale, au lieu de deux semaines de délais à prévoir auparavant.
Une réduction du poids des pièces de plus de 50% grâce à l’utilisation de la technologie FDM® haute performance de Stratasys par rapport à l’outillage aluminium traditionnel. L’efficacité et le rendement rapide du système de production Fortus 380mc permet à Hager Group d’optimiser les processus de production et de réduire les temps d’arrêt.
Hager Group est un des principaux fournisseurs leaders en matière de solutions et de services pour les installations électriques et couvre la distribution d'énergie électrique, les solutions de compteurs, des dispositifs de contrôle et protection, le cheminement de câbles et câblage, les systèmes d’automatisation des bâtiments ainsi que les dispositifs de sécurité tels que les alarmes et les détecteurs de mouvement et d’incendie.
Son site de production à Saverne en France compte 350 salariés et se spécialise dans l’automatisation de bâtiments et les systèmes de gestion d’énergie.
Au cœur de sa quête constante d’innovation pour optimiser la réactivité, réduire les délais et coûts de production, le site de Saverne de Hager Group a évalué les solutions de fabrication additive. L’entreprise a alors investi dans un système de production FDM de Stratasys via le revendeur de Stratasys France CADVision pour répondre facilement et de manière rentable à leurs besoins d’outillage.
Nécessitant un système facile d’utilisation, apportant sécurité pour le personnel et qui permette de maintenir la cadence de production, l’équipe a choisi le système de production Fortus 380mc. Cette imprimante 3D haute performance permet à l’entreprise de travailler avec des matériaux thermoplastiques de niveau industriel.
« À Hager Group, nous devons créer des pièces complexes – ce qui prend du temps et est coûteux à réaliser avec les méthodes d’usinage traditionnelles, et qui n’est pas toujours faisable avec toutes les solutions de fabrication additive sur le marché, » explique Alexandre Callegher, Développeur Mécanique chez Hager Group.
« En installant un système de production Fortus 380mc sur le site, nous avons désormais accès à une technologie de pointe qui nous fournit des résultats fiables tout au long du processus d’outillage. »
Auparavant, lorsque l’équipe devait remplacer ou fabriquer un outil sur le site, les longs délais de la sous-traitance ne leur permettait pas d’être assez réactif. Cela pouvait engendrer des risques de temps d’arrêt sur la production, ainsi que des surcoûts et ralentir la productivité.
« Nous avions besoin de créer des pièces complexes, fonctionnelles et légères de manière rapide et rentable à la fois – c’est là où la fabrication additive s’intègre parfaitement à notre pratique. C’est la raison pour laquelle nous l’avons intégrée à toutes nos opérations sur le site de Saverne.
Imprimer les pièces en 3D nous a permis de réduire considérablement nos coûts de production par rapport à l’usinage en aluminium, mais aussi de réduire de 50% leur poids. Nous La fabrication additive permet à l’équipe d’imprimer en 3D des outils légers grâce à la réalisation de structures en nids d’abeille.avons déjà vu un retour sur investissement en 18 mois seulement. »
La Production d’Outillage plus Rapide, plus Légère et plus Efficace
Traditionnellement, les outils étaient produits en aluminium, ce qui était coûteux et long à réaliser. Cela laissait l’équipe avec peu de flexibilité et de marge d’erreurs dans le cas où des changements de design étaient nécessaires.
En apportant sur le site un système aussi performant et orienté vers la production, l’équipe peut réagir rapidement aux demandes d’itérations des pièces, tout en épargnant du temps et des coûts vitaux. En effet, les designers ont gagné trois jours de délais car la fabrication additive permet d’ôter des étapes de design et les contraintes mécaniques issues des méthodes soustractives avec les métaux.
« Dorénavant, nous produisons régulièrement des pièces d’outillage imprimées en 3D, personnalisées et en faible volume, sur place dans les 24 heures de la requête initiale des ingénieurs – à une fraction de coût et de poids par rapport aux pièces en aluminium, » dit Callegher.
« Avec la sous-traitance de la fabrication d’outillage que nous utilisions auparavant, le procédé nous prenait deux semaines. Aujourd’hui, nous utilisons des matériaux haute performance et nous pouvons fabriquer des outils sur mesure pour des tâches spécifiques avec une qualité répétable et fiable. »
La réduction de poids par outil est un avantage supplémentaire de la technologie FDM pour l’équipe. La production de bras de préhension sur le site en est un exemple. Auparavant, un bras de préhension était fabriqué en plusieurs pièces. Le design était complexe et il était difficile d’assembler toutes les pièces.
Dans le but de réduire le poids de l’outil, l’équipe devait creuser et extraire manuellement le matériau superflu de la pièce pour le rendre plus léger et ainsi aider les ingénieurs et opérateurs sur le site de production. La fabrication additive FDM a accru la capacité de l’équipe à imprimer des outils légers en produisant des structures en nid d’abeille en une fraction de temps et de coût par rapport aux procédés d’usinage classiques.
“Chaque outil que nous fabriquons a une caractéristique différente et souvent des exigences particulières. Nous utilisons principalement le matériau ABS-M30™, et le matériau Nylon 12™ qui est robuste pour tester les performances d’une pièce mécanique sous haute pression.
Cela dit, contrairement à beaucoup d’imprimantes 3D sur le marché, la Fortus 380mc nous offre la possibilité de choisir parmi une large gamme de matériaux selon les applications requises, ” ajoute Callegher. « Le large plateau de la machine nous permet également de lancer plusieurs projets en même temps. »
Récemment, l’équipe était chargée de remplacer le support rotatif d’une antenne, essentielle pour tester la fréquence Bluetooth. Le support d’antenne original ne convenait pas dû à son manque de résistance et de stabilité. L’équipe l’a donc Un support rotatif imprimé en 3D avec la Fortus 380mc, pour une antenne de test de fréquence Bluetooth.remplacé rapidement en se tournant vers la fabrication additive.
“Avant même de penser à l’usinage en aluminium, nous avons utilisé la Fortus 380mc pour imprimer en 3D la pièce finale en ABS-M30,” explique Callegher. “Cela nous a permis de créer un outil de travail précis plutôt qu’une pièce complexe qui nous aurait pris trop de temps à produire avec les méthodes traditionnelles.
Au lieu de deux semaines de production, cela a pris une nuit pour imprimer la pièce finale en entier. Cela a été vital pour optimiser et apporter plus de flexibilité au processus de conception de la pièce.”
Au-delà de la Production d’Outillage
En vue des avantages à utiliser la technologie de Stratasys, Hager Group envisage à présent d’aller au-delà de la production d’outillage.
« La technologie FDM a transformé notre façon de travailler, à tel point que nous sommes sur le point de lancer sur le commerce une petite série de produits avec des composants en 3D. Sur les deux années à venir, nous prévoyons d’imprimer en 3D 120 capuchons de petite taille avec un composant électronique fixé dedans avec une résine.
Avant notre investissement, nous n’avions pas idée de ces avantages commerciaux. La fabrication additive de Stratasys nous a ouvert les yeux sur la façon dont nous pouvons entièrement déployer nos activités ici à Saverne, » conclut Callegher.
Il est également incontournable pour Hager Group d’avoir une équipe dédiée à la fabrication additive pour atteindre ses objectifs.
Callegher conclut : « Le distributeur de Stratasys, CADVision, est un partenaire de confiance dont l’expertise nous a permis d’optimiser notre utilisation de la technologie de fabrication additive FDM et de l’appliquer à un large panel d’applications. Ce soutien et expertise de haut niveau est d’autant plus valable à l’heure où nous continuons nos efforts vers d’autres aires d’applications. »
www.hagergroup.com