Moins de temps d'arrêt grâce au contrôle des mesures en cours de processus.
Selon Renishaw, les capteurs de mesure, les systèmes de mesure et les solutions d'étalonnage sont la base d'une production optimale et d'une qualité élevée et constante de chaque ouvrage.
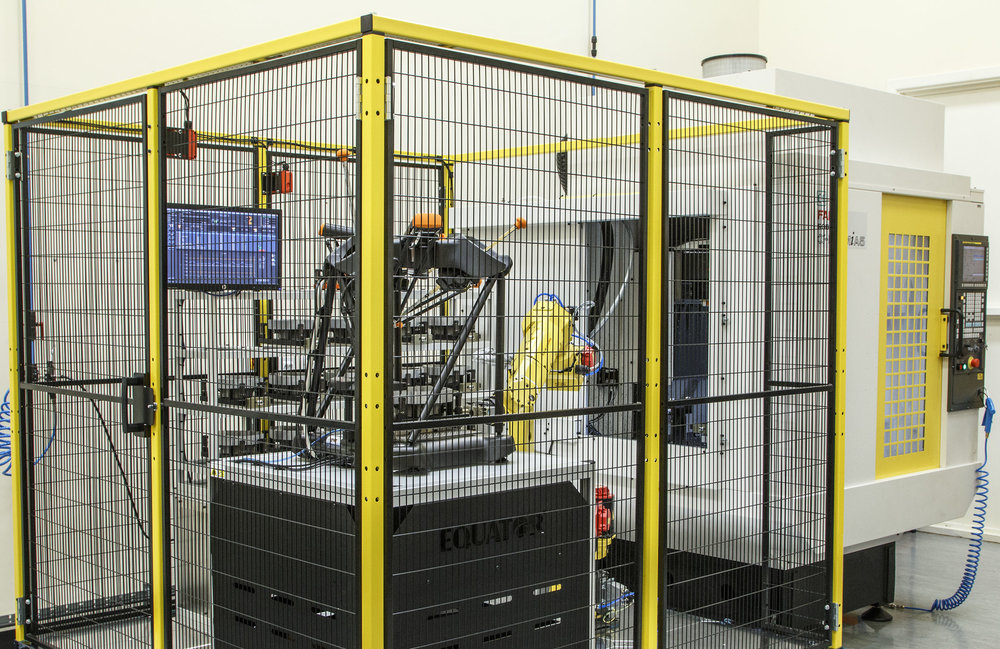
Ceci est particulièrement vrai pour une production entièrement automatisée. Renishaw propose diverses solutions permettant aux entreprises d'optimiser progressivement leur production au moyen d'une technologie de mesure.
Actuellement, les usines entièrement automatisées et dites « intelligentes » sont souvent discutées. Pour ce réaliser, les systèmes de mesure et les capteurs sont indispensables dans les machines d'usinage. Les capteurs de mesure et les systèmes laser peuvent détecter des problèmes, tels que les bris d'outil, l'usure ou les écarts de dimension de la pièce sur la machine.
Grâce à un retour direct des données de mesure au système de contrôle CNC, une intervention immédiate peut être réalisée. De cette façon, la défaillance et les coûts indésirables peuvent être évités à l'heure. Tous les produits Renishaw sont axés sur le contrôle du processus et l'usinage répétitif de produits de précision.
En outre, des solutions telles que sondes de mesure, les temps de réglage et de cycle raccourcissent la fabrication en mettant les pièces en place et en inspectant les processus en cours automatiquement.
Démonstration de cellule de production
Aux salons et dans l'espace de démonstration à Breda, Renishaw montre ce processus aux clients en utilisant une cellule de production complète. La cellule de production comprend une machine d'usinage, un robot, divers systèmes de mesure dans la machine d'usinage et le système de mesure Equator™ de Renishaw.
L'objectif de cette installation est de démontrer comment différentes technologies peuvent contribuer ensemble à accroître la productivité et les capacités de production. Outre les capteurs de mesure et les systèmes de mesure des outils et d'alignement de la pièce à usiner, la cellule est équipée d'un Equator permettant d'effectuer des mesures comparatives.
L'Equator compare les produits avec un « master » comme référence. Parce que le « master » se trouve dans le même environnement que les pièces, l'Equator peut mesurer les produits tout en compensant les variations dues aux conditions thermiques. En combinaison avec le logiciel, le processus peut être surveillé et ajusté en permanence, de sorte que les dimensions du produit restent dans les mesures de tolérance.
En fait une cellule de production à correction automatique est créée pour la production automatique et sans intervention humaine de petites séries.
Appliqué dans sa propre usine
Avec sa propre usine en Angleterre, Renishaw peut démontrer que les systèmes de mesure en production ont un effet positif sur la productivité. Renishaw produit sa gamme de produits dans une usine entièrement automatisée comprenant plus de 300 machines à commande numérique. Les produits qu'ils proposent sur le marché sont également utilisés par Renishaw pour optimiser la production.
Toutes les machines de production sont équipées de capteurs de mesure et de systèmes de mesure pour le contrôle des outils et des pièces à usiner. De nombreux produits vendus par la société ont été développés pour fournir une solution aux questions venant de leur propre usine. Et dans cette usine, les nouveaux produits sont minutieusement testés et appliqués avant d'être proposés sur le marché. C'est pourquoi Renishaw est convaincu que la gamme de produits est pertinente et intéressante pour ses clients.
Pyramide de processu
« De plus en plus, les fabricants se rendent compte des avantages du contrôle de processus, car ils optimisent d'avantage le processus de production en termes de rapidité, de flexibilité, de qualité, de répétabilité et de réduction des coûts. La gamme de produits de Renishaw prend en charge tout le spectre des applications de métrologie industrielle. Afin de clarifier et d'aider les fabricants à intégrer les mesures sur la machine, nous avons mis en place une pyramide de processus.
Cette pyramide comprend quatre phases et indique, pour chaque phase, ce qui doit être fait pour passer par le trajet de contrôle du processus », déclare Hans van Rossum, responsable des ventes pour le Benelux chez Renishaw.
La première phase de la pyramide constitue la base du processus. Au cours de cette phase, Renishaw mettra au point le processus de production chez le client. Nous examinons la géométrie de la machine et ses éventuels défauts. La première phase doit garantir la production dans des conditions stables. L'étalonnage des performances statiques et dynamiques d'une machine est effectué à l'aide d'un interféromètre laser et de systèmes de mesure à bras sphérique.
Un développement récent est le calibreur multiaxe XM-60, qui intègre à la fois des erreurs linéaires et des erreurs d'angle et de rectitude. Le système peut également prendre en compte la température ambiante. Le XM-60 est particulièrement utile lors du calibrage de centres d'usinage à cinq axes. Plus tard, ces solutions peuvent également être utilisées pour des contrôles périodiques. Ensuite, par exemple, la croissance des défauts dans la machine peut également être mesurée.
La base est essentielle
« Les bases doivent être fiables avant que nous puissions tirer le meilleur parti des phases successives », déclare Rob Reuter, responsable régional des ventes chez Renishaw. Il poursuit : « La deuxième phase représente le réglage de processus. Cette phase concerne la détermination de l'emplacement du produit (comment mon produit est-il positionné ?) et des données des outils (les outils sont-ils présents ? Quelles sont la longueur et le diamètre de l'outil ?).
Les clients utilisent principalement des sondes pour réinitialiser le point zéro, tandis qu'une sonde peut être utilisée pour de nombreuses autres actions. La deuxième phase répond à ces questions.
Le contrôle en cours de traitement est réalisé dans la troisième phase. Une entreprise d'usinage doit être bien organisée avant qu'un contrôle automatisé puisse avoir lieu pendant le processus d'usinage. Dans la troisième phase, les différentes sources de variation sont vérifiées à l'aide notamment de sondes en cours d'usinage. Pensez à l'usure de l'outil, aux variations de température et aux dimensions de la pièce.
Ces données peuvent être renvoyées au processus, après quoi tous les décalages peuvent être ajustés automatiquement, tout en continuant la production. Le système peut également choisir d'arrêter la production, par exemple en cas de rupture d'outil ».
Quatrième phase
La quatrième et dernière phase de la pyramide des processus est la surveillance des processus. La surveillance des processus se concentre sur les activités de surveillance et de rapports d'activités qui fournissent des informations sur les résultats des processus terminés. Ces informations peuvent être utilisées pour influencer positivement les activités ultérieures. Ici, l'Equator est pratique dans une cellule de production automatisée.
De plus, l'inspection finale des pièces usinées est généralement effectuée sur une CMM. Mesurer sur une CMM est un processus qui prend du temps et dans de nombreuses entreprises, il s'agit d'un ralentissement de la production. Afin d'accélérer ce processus et de pouvoir mesurer des produits encore plus complexes dans une chaîne de production, Renishaw a développé le REVO-2. Le système REVO© utilise des mouvements synchronisés et une technologie de mesure à cinq axes.
Ceci garantit que la CMM produit moins de mouvements et ne souffre pas d'effets dynamiques à des vitesses de mesure rapides. Pour ce faire, la tête REVO-2 effectue des mouvements lents tandis que la CMM se déplace de manière linéaire lente. Grâce au REVO-2, vous pouvez économiser jusqu'à cinquante pour cent du temps.
« Comme vous pouvez le constater, Renishaw propose des produits adaptés à chaque phase de la pyramide des processus. Une étude de faisabilité montre que dans un processus intelligent avec contrôle intelligent, le nombre de pertes et de réusines est 60 000 fois moins élevé lorsque uniquement les paramètres du processus sont observés », explique Van Rossum.