www.industrieweb.fr
16
'15
Written on Modified on
Qualité jusqu’au moindre détail dans l’usinage de blisks et aubes de turbine
La technologie de frettage Haimer enrichit les centres d’usinage Starrag de précision.
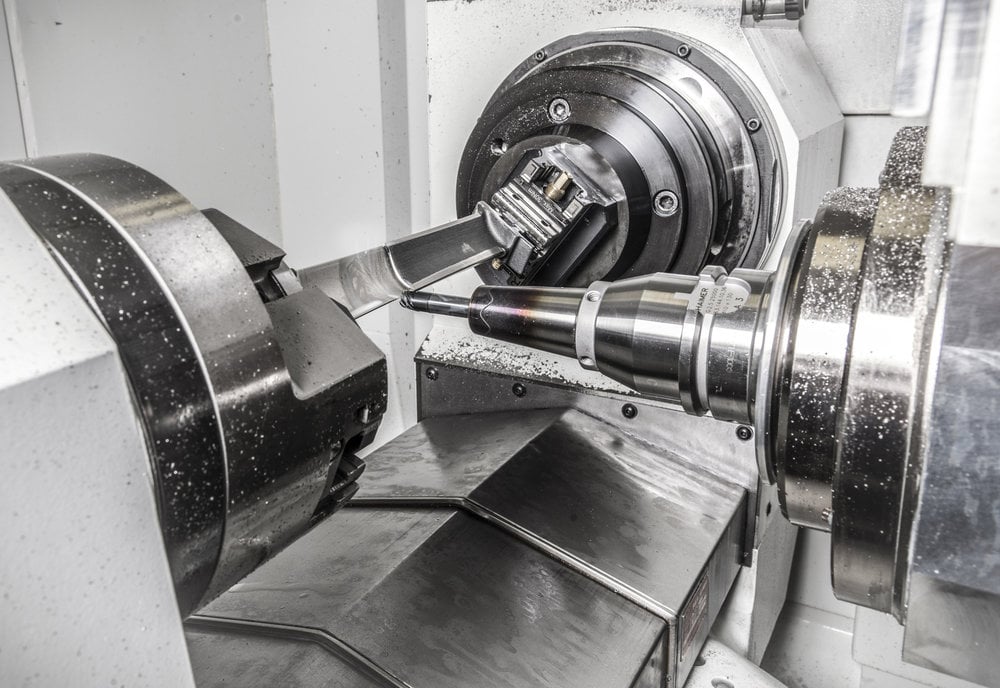
La marque Starrag a ses origines au siège du Starrag Group à Rorschacherberg en Suisse (plus d’informations sur la société dans l’encadré à la fin du texte). Son marché cible est l’industrie aéronautique et le secteur de l’énergie et elle offre des centres d’usinage cinq axes à grande performance d’enlèvement pour l’usinage d’aubes de turbine, rotors, systèmes « aubes et disque combinés » et composants complexes de très grande précision.
Depuis le début du 20ème siècle, l’industrie aéronautique fait partie des marchés principaux pour les machines-outils Starrag se caractérisant déjà à cette époque par une construction rigide et solide et par leur grande exigence technologique. De ce fait, il est peu étonnant que Starrag ait compté parmi les pionniers de l’usinage simultané en cinq axes dans les années 60. Une longueur d’avance en matière de savoir-faire qui se manifeste aujourd’hui dans la gamme exigeante de produits. Elle comprend des types de machines comme les séries STC et BTP pour l’usinage de titane. De plus, la gamme est complétée par les centres NB spécialisés dans l’usinage des blisks et par la série LX, développée pour l’usinage simultané cinq axes très précis et efficace d’aubes de turbine.
„Nos machines sont situées dans la catégorie supérieure en matière technologique », précise Patrik Rutishauser, Responsable Application Engineering. « Elles se caractérisent par un maximum de performance et précision. En outre, nous offrons à nos clients une plus-value particulière concernant l’application. » Starrag se voit en tant que partenaire technologique pour les utilisateurs et est capable de concevoir et réaliser des processus complets. « Si un client vient nous voir avec un composant dont il lui faut 10.000 pièces, nous planifions l’équipement intégral et livrons la machine avec le logiciel, les dispositifs de serrage, les porte-outils ainsi que les appareils périphériques. »
Une telle offre supplémentaire n’est possible que grâce aux expériences faites dans le développement de machines-outils, systèmes CAM et outils spéciaux pendant des décennies – et grâce au savoir-faire que Starrag a recueillit par exemple dans l’usinage de prototypes et petites séries d’aubes de turbine. Patrik Rutishauser est le responsable de ce domaine : « Mon travail consiste dans le développement technologique et logiciel pour les soi-disant Single Blade Applications. Dans mon équipe, travaillent les techniciens d’application et développeurs main dans la main. Ainsi, on peut réaliser rapidement et sans détour exactement ce dont l’utilisateur a besoin. »
Expériences de la production
Ses employés font des expériences importantes dans le CPE (Center of Production Excellence), le centre d’application de Starrag à Rorschacherberg où ils testent et optimisent de nouveaux processus de fabrication exigeants. Le hall de 2000 m² est équipé de centres d’usinage Starrag quatre et cinq axes modernes. L’équipe des applications y exécute diverses opérations d’usinage allant de l’usinage lourd d’alliages de titane très résistants à l’usinage de grande vitesse des métaux légers. Patrik Rutishauser souligne : « Nous travaillons des pièces de rotation, des pièces cubiques complexes ainsi que des surfaces d’écoulement – dans les conditions de production ! Nous y fabriquons également des séries pilotes et petites séries pour nos clients. Cela signifie une production conforme aux dessins et à la qualité au prix compétitif. » Selon le spécialiste des applications c’est un avantage car on peut gagner un savoir-faire précieux - allant jusqu’au moindre détail - autour des exigences de la machine et de l’intégralité du processus de fabrication. «Ce n’est pas comme lors d’une présentation client », rajoute Rutishauser, « où on peut passer sur certains petits détails. »
Détail important: le serrage d‘outils
Nous savons depuis longtemps chez Starrag quelle importance attribuée au serrage d’outils dans l’usinage de précision. Il y a 20 ans, des broches à rotation rapide de 30.000 min-1 ont été utilisées à Rorschacherberg. A l’époque, les outils avaient été serrés à l’aide de mandrins à pince, mandrins Weldon et Whistle Notch traditionnels, ce qui a mené à bien de problèmes dû à l’insuffisante concentricité. Car lors des grandes vitesses de rotation, la moindre dérivation détériore les résultats de fraisage et l’état de surface tout en accentuant l’usure de l’outil et de la broche. De plus, la géométrie de ces mandrins accuse de trop grands contours d’encombrement, pour pouvoir atteindre les cavités profondes avec des courts outils de serrage.
Starrag en a tiré des conséquences en basculant aux mandrins de frettage, offrant ainsi une meilleure concentricité et moins d’encombrement grâce à leur corps de serrage symétrique en rotation. Lors des premiers essais avec cette nouvelle technique de serrage, Starrag a encore dû lutter contre certaines faiblesses : A l’époque, les mandrins avaient été chauffés à l’aide d’air chaud ce qui nécessitait beaucoup de temps et signifiait une forte sollicitation du matériel.
Il y a presque 15 ans et à la recherche d’améliorations, les spécialistes d’application de Starrag sont tombés sur la société Haimer GmbH à Igenhausen qui est aujourd’hui le leader européen dans le serrage d’outils. «Haimer a professionnalisé le frettage d’outils », accentue Patrik Rutishauser. « Déjà à cette époque-là, la société a proposé une grande variété en mandrins de frettage ainsi qu’un banc de frettage à bobine inductive et capsules de refroidissement qui pouvait être utilisé facilement par tout le monde. Jusqu’à ce jour, Haimer a continué à développer d’une manière permanente sa gamme de porte-outils et machines de frettage et est resté fidèle à ses grandes exigences en matière de qualité. De temps à autre, nous évaluons différents systèmes et fabricants mais les produits Haimer restent imbattables en termes de précision et qualité. En général, nous apprécions avec la technique de frettage la possibilité de serrer des outils avec longueur de sortie courte et bien sûr les fins contours par rapport à d’autres systèmes de serrage.
Le détail est aussi important pour les mandrins de frettage
Ce n’est pas pour rien que la philosophie de l’entreprise familiale Haimer s’appelle « La Qualité Gagne ». L’idée derrière ce slogan est le fait de fabriquer uniquement au siège d’Igenhausen près d’Augsbourg où on peut contrôler la précision à 100%. Tous les mandrins de frettage – ainsi que les versions standard – y sont fabriqués d’un acier réfractaire spécifique et équilibrés à G2.5 à 25.000 tr/min ou <1gmm balourd résiduel. Les surfaces fonctionnelles sont rectifiées avec précision et les tolérances du cône encore plus précises que prescrites par les normes en vigueur.
Pour les exigences d’usinage particulières, Haimer propose des mandrins de frettage spécifiques. Les Power Shrink Chucks par exemple sont adaptés spécialement aux applications de fraisage de grande vitesse et précision. Le design breveté combine une faible tendance aux vibrations avec une grande rigidité et une conception fine au bout du mandrin. Cette forme particulière permet à l’utilisateur d’augmenter la profondeur de coupe et les avances afin d’atteindre un plus grand taux d’enlèvement tout en garantissant une bonne qualité de surface. Les Haimer Heavy Duty Shrink Chucks sont conçus pour de grands outils lors de l’usinage lourd. Ils disposent de côtes renforcées dans la zone de serrage, de contours extérieurs rigides ainsi que de rainures de dilatation brevetées au niveau de l’alésage de serrage. On obtient ainsi de grandes forces de serrage qui se laissent comparer à celles des mandrins à serrage fort. Le portfolio de porte-outils de frettage est complété par les petits Haimer Mini Shrink Chucks. Il s’agit de mandrins de frettage monobloc avec un design extrêmement fin et un contour extérieur à 3° - conçus pour les moulistes.
Matériaux difficiles, grandes exigences de l’état de surface
Cette variété constitue un avantage pour Patrik Rutishauser. Il s’explique : «L’usinage d’aubes en profilés extrudés comprend en règle générale deux processus. Il y a d’abord l’ébauche. Il y est important que le mandrin ait une composante amortissante afin de permettre une profondeur de coupe et des avances maximales et d’avoir un haut taux d’enlèvement en une seule opération. Ensuite et lors de la finition, il n’y a pas de grandes forces qui entrent en jeu. Ici, une très bonne concentricité et la classe d’équilibrage sont importantes. Les Power Shrink Chucks de Haimer sont adaptés d’une manière optimale à ces deux processus d’usinage. Et si nous devons faire face à une ébauche encore plus importante, nous recourons aux Heavy Duty Chucks. »
En ce qui concerne la qualité des mandrins de frettage, Starrag ne se satisfait que de la meilleure qualité. Car le titane et les autres matériaux difficilement usinables imposent de grands efforts à l’interface et à la bobine durant l’ébauche et la finition. « Ce qui compte en fin de compte, c’est la qualité de la pièce », précise Patrik Rutishauser, « la qualité doit convenir à partir de la première pièce, car l’ébauche en titane elle-même coûte déjà une fortune. Et nous sommes convaincus que la qualité des porte-outils se reflète 1 :1 dans la qualité de la pièce. » Ceci est très vraisemblable pour l’état de surface, qui représente un facteur important. Les aubes de turbine nécessitant une structure très fine afin d’être énergétiquement parlant efficace. Aujourd’hui, elle peut être atteinte grâce au fraisage, sans processus d’affûtage complémentaire. Pour l’instant, Starrag est capable d’atteindre des qualités de surface de Ra=0,8 µm – les 0,4 µm sont déjà à portée de main.
Machines de frettage haut de gamme garantissent un serrage d’outils rapide et facile
Pour le frettage de ses outils, Starrag possède dans son centre d’application un banc de frettage Haimer Power Clamp Profi Plus NG. Une machine à l’aide de laquelle on peut fretter et défretter tous les outils HSS et carbure à tolérance de queue h6 et d’un diamètre 3mm à 50mm en très peu de temps. Elle est équipée du système breveté de double bobine ce qui signifie que la bobine s’adapte à la longueur et au diamètre du mandrin de frettage. Seule la zone de frettage est chauffée ce qui réduit nettement le temps de chauffe et de refroidissement réalisé par un refroidissement par contact. A côté de ce banc, on trouve la solution haut de gamme pour le frettage et le refroidissement professionnels : une machine Haimer Power Clamp Premium, offrant une grande surface de travail, une manipulation simple, des capsules de refroidissement à guidage linéaire ainsi qu’un système de surveillance de température. Le banc chez Starrag dispose également d’un système de préréglage de longueur – précis à 0,02mm près – parce que les outils doivent toujours être frettés à une longueur définie.
„Les mandrins et machines de frettage de Haimer sont du standard chez nous“, explique Patrik Rutishauser, „car ils offrent les conditions parfaites pour un usinage fiable comme on nous le demande. Ces produits ne sont pas uniquement utilisés dans notre CPE, mais nous les vendons également avec nos machines, quasiment au catalogue. De ce point de vue, il est très important que la qualité des produits livrés soit constante. Avec Haimer, nous pouvons en être sûr. Je ne peux pas me souvenir qu’un mandrin a jamais été objet d’une réclamation client.
Pour chaque exigence la machine-outil adaptée
Le Starrag Group (env. 1617 employés et un CA de 390 Mio. CHF en 2014), un des leaders technologiques mondiaux dans la fabrication de machines-outils, regroupe les marques Berthiez, Bumotec, Dörries, Droop+Rein, Heckert, Scharmann, SIP, Starrag, TTL et WMW. Sur différents sites, on construit une large palette de machines pour le fraisage, tournage, perçage et affûtage de pièces en métal, matériaux composite et céramique avec des spécialités pour chaque marque. La gamme allant du petit centre d’usinage de Bumotec, approprié à l’usinage de pièces d’horlogerie et d’ordinateur jusqu’à la machine Gantry de Droop-Rein, remplissant d’une longueur de plusieurs mètres des halls entiers et qui est adaptée à l’usinage de grandes pièces lourdes. Parmi les clients comptent avant tout des entreprises internationales situées dans les trois marchés cibles : Aerospace & Energy, Transportation & Industrial Components et Precision Engineering. Le portfolio de machine-outils est complété par des prestations et services technologiques et permet aux clients des progrès substantiels en matière de productivité.
En tant que partenaire à long terme de l’industrie aéronautique, le Starrag Group dispose de la compétence de développer des solutions exigeantes pour l’usinage de composants de turbine. Un élément standard de ces équipements complets est la technologie de frettage de Haimer. Images: Starrag
Les Power Shrink Chucks de Haimer sont utilisés lors d’opérations d’ébauche et de finition exigeantes chez Starrag. Images : Haimer
Les Heavy Duty Shrink Chucks de Haimer atteignent de grandes forces de serrage grâce aux côtes renforcées dans la zone de serrage et autres caractéristiques constructifs. Ils sont adaptés à l’usinage lourd avec de grands outils.
Patrik Rutishauser, Responsable Application Engineering, est convaincu des mandrins et machines de frettage de Haimer: “Haimer a professionnalisé le frettage d’outils. »
Pour le frettage d’outils, Starrag dispose dans son CPE d’une Haimer Power Clamp NG (à gauche) et d’une Power Clamp Premium. Tous les deux bancs sont équipés d’une double bobine brevetée s’adaptant à la longueur et au diamètre du mandrin de frettage.
Solution haut de gamme pour le frettage et le refroidissement: Le banc Haimer Power Clamp Premium offre une grande surface de travail, une manipulation simple, des capsules de refroidissement à guidage linéaire ainsi qu’un système de surveillance de la température. Le système de préréglage optionnel est intégré dans le banc de Starrag.
A proximité des bancs de frettage se trouve une équilibreuse Haimer Tool Dynamic Preset, une solution combinée pour l’équilibrage et la mesure pour porte-outil et outil. Cette machine est utilisée d’une façon permanente pour les outils fabriqués par Starrag, tout particulièrement les outils étagés.