www.industrieweb.fr
03
'13
Written on Modified on
NORD DRIVESYSTEMS fournit de puissants systèmes d’entraînements pour le brasseur le plus moderne d’Europe
En 40 ans d’activité ininterrompue, 24 h sur 24, les citernes et cuves de l’ancienne salle de brassage de la brasserie de bières Forst (Italie) ont produit 25 millions d’hectolitres de bière. Aujourd’hui, avec l’évolution des techniques de brassage, notamment en matière énergétique, la direction a décidé de construire une salle de brassage entièrement nouvelle, devant fonctionner de manière extrêmement efficace, dans le respect des dernières normes de sécurité et produisant les plus faibles émissions possibles. Dès la première semaine de mise en service, la brasserie a réduit sa consommation d’énergie de 30%.
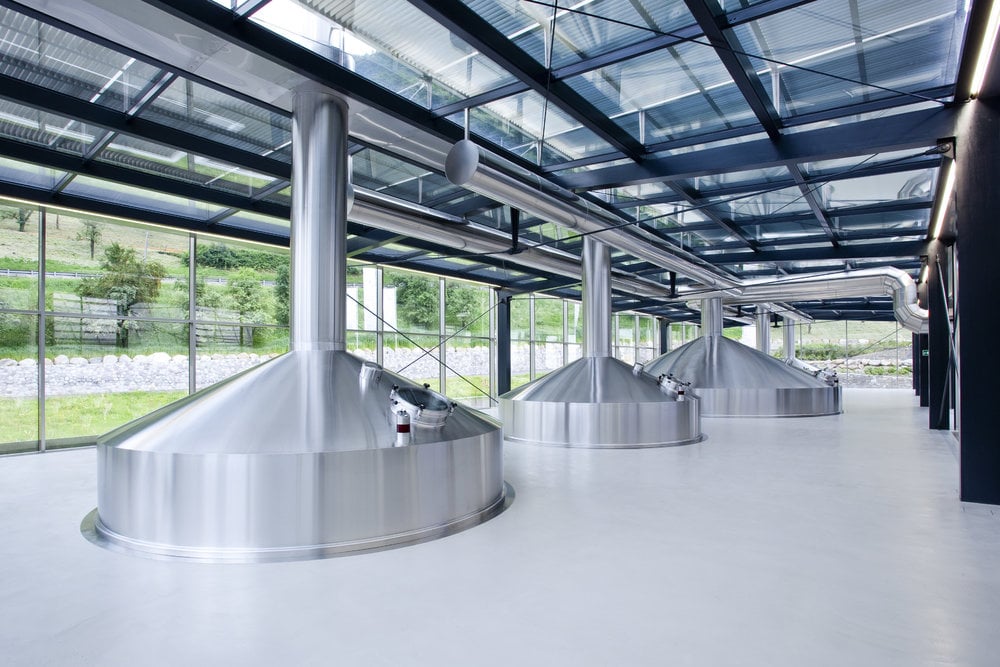
4 800 m² offre une vue sur la brasserie, considérée comme un modèle du genre en Europe. Elle peut produire jusqu´à douze brassages par jour, d´un volume de 630 hectolitres chacun. La capacité annuelle de production atteint 900 000 hl.
Des systèmes d´entraînement spécifiquement adaptés aux tâches à effectuer
NORD DRIVESYSTEMS a assemblé les motoréducteurs en fonction des exigences spécifiques des cuves des différentes applications, du moulin qui broie doucement le malt au début du processus de brassage, au convoyeur à vis qui enlève les drêches. En phase initiale, le malt est mélangé dans les cuves de brassage à de l´eau de source provenant des montagnes environnantes. Le mélange est ensuite chauffé à différentes températures au moyen de surfaces conductrices thermiquement optimisées dans la partie basse et de
l´ossature de la cuve de clarification. Un motoréducteur à couple conique contrôlé par variateur de fréquence NORD équipé d´un capteur de température, entraîne l´agitateur à l´intérieur de la cuve. Le liquide est ensuite envoyé par pompage dans la cuve de clarification.
Ajustement en douceur de la vitesse de clarification
D´un diamètre de 8,6 mètres et d´un poids de près de 21,5 tonnes, la cuve de clarification constitue le coeur de la salle de brassage. Le liquide et les parties solides du brassin sont séparés selon des process entièrement automatisées. En se déposant au fond de la cuve, les drèches forment une couche filtrante naturelle. Un hacheur spécial desserre cette couche afin d´assurer l´écoulement optimal du moût. Ainsi, la qualité du moût progresse et les matières premières sont utilisées de manière efficace. Des capteurs de pression au bas du récipient détectent la consistance du moût, et l´entraînement ajuste la vitesse de la machine en conséquence. Ce système de contrôle intelligent garantit des débits de 9 à 14 litres par minute et par mètre carré. Ensuite, le moût est enlevé : la machine est graduellement abaissée et les barres plates montées sur ses six bras éjectent le moût de la cuve à travers une trappe. Cette étape est aussi entièrement automatique. En cas de trop forte accumulation de matière, l´abaissement s´arrête et la vitesse est ajustée. Ainsi, la cuve peut être vidée en six minutes maximum. Afin de traiter la substance tout en douceur, le moût est relâché à basse vitesse. Mais lorsque le moût est enlevé, une vitesse élevée est indispensable pour vider la cuve aussi rapidement que possible. Ainsi, l´opacité des drêches est minimale et l´écoulement, très efficace. Pour vérifier si le système fonctionne correctement, la vitesse, la consommation de courant et la température du moteur font l´objet d´un suivi centralisé permanent. Les deux tâches sont gérées par système d’entrainement NORD adapté avec un arbre creux cannelé. L´entraînement est constitué d´un moteur électrique, d´un réducteur industriel et d´un motoréducteur à couple conique. Il présente un couple maxi de 96 000 Nm et peut réguler en continu la vitesse circonférentielle d´un à cent mètres par minute, le tout en fournissant un couple constant.
Précision au millimètre
A l´intérieur de la cuve de clarification, le hacheur se soulève et s´abaisse avec une amplitude maxi de 500 mm. Le dispositif de levage opère avec une précision de l´ordre du millimètre, même à pleine charge. Un capteur de fin de course et un capteur optique ont été installés pour un positionnement exact. La hauteur est réglable à l´arrêt, en phase de ralenti, et en fonctionnement. A cette fin, le réducteur à couple conique et
l´unité de levage à huile hydraulique sont tous deux conçus pour supporter les charges axiales et radiales engendrées lors du processus. Le moteur d´entraînement offre une puissance nominale de 18,5 kW et fournit des vitesses de sortie de 0,04 à 4 tr/min. Pour garantir le maintien de la vitesse requise, le moteur est pourvu d´un codeur. Un ventilateur externe assure le refroidissement du moteur à basse vitesse. Les deux réducteurs sont pourvus de réservoirs d´expansion d´huile pour empêcher le lubrifiant de s´échapper à haute température par les clapets d’évent. Un système joint spécifique sur le réducteur industriel garantit la présence constante d´une pellicule lubrifiante suffisante sur l´arbre. Grace à cette conception, la cage de levage ne nécessite aucun réservoir d´huile supplémentaire, ce qui élimine tout problème d´étanchéité. Selon le principe monobloc UNICASE développé par NORD, tous les paliers sont intégrés dans un seul et même carter garantissant un excellent niveau de solidité et rigidité. Les carters monoblocs UNICASE sont dépourvus de joints d´étanchéité qui pourraient dévier sous l´effet du couple ou des forces radiales. Les réducteurs compacts et légers fonctionnent sans bruit, en offrant une longévité supérieure et une consommation d´énergie inférieure par rapport à des réducteurs avec une conception de carter différente.
La technologie moderne réduit la consommation de vapeur de 47%
« En construisant la nouvelle salle de brassage, nous voulions nous assurer que les ressources seraient traitées le plus en douceur possible », fait observer le Dr. Walther Unterthurner, Directeur Technique de la brasserie Forst. « En outre, nous voulions utiliser ces technologies modernes pour réduire fortement la consommation d´énergie et les émissions ». En conséquence, outre les installations efficaces de la salle de brassage, un nouveau système de récupération de chaleur a été intégré dans le condensateur de vapeur. La chaleur nécessaire à la production du moût de bière est stockée dans un grand réservoir d´énergie sous la forme de citernes d´eau chaude à l´arrière du bâtiment et réutilisée par les process de brassage en aval. Selon Walter Unterthurner, ces différentes mesures se traduisent déjà par une baisse de consommation
d´énergie de 30%. « Notre objectif est de réduire la consommation de vapeur d´au moins 47% », poursuit-il.
Illustration 1 : La nouvelle salle de brassage offre une capacité annuelle de 900 000 hectolitres de bière. Elle peut produire jusqu´à 12 brassages par jour, d´un volume de 630 hl chacun.
Illustrations 2, 3 : Chaque système d´entraînement a été adapté aux besoins spécifiques de l´application. Ici, un motoréducteur à couple conique alimentant la cuve de clarification.
Illustration 4 : Un seul motoréducteur à arbres parallèles entraîne le convoyeur à vis.
Illustration 5 : D´un diamètre de 8,6 mètres, la cuve de clarification constitue le coeur de la salle de brassage. Ici, le moût est automatiquement séparé des drêches.
Illustration 6 : Un seul système d´entraînement commande le processus de clarification, aussi bien le relâchement des drêches que la clarification de la cuve. En associant un motoréducteur et réducteur industriel, on atteint des couples de 96 000 Nm.
Illustration 7 : Le motoréducteur à couple conique est couplé à un réducteur industriel basé sur un arbre creux cannelé.
Illustration 8 : « La nouvelle salle de brassage est un projet phare conçu pour fonctionner en toute fiabilité pendant au moins 40 ans », explique le Dr Walter Unterthurner, Directeur Technique de la brasserie de Forst (ici à gauche, aux côtés du maître brasseur Manfred Biechl).
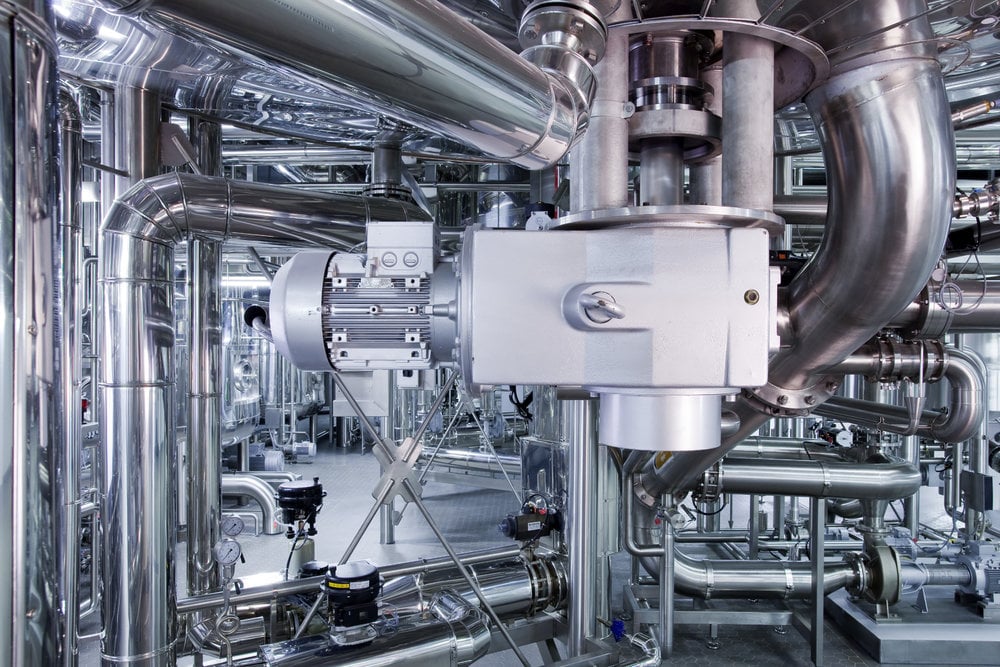
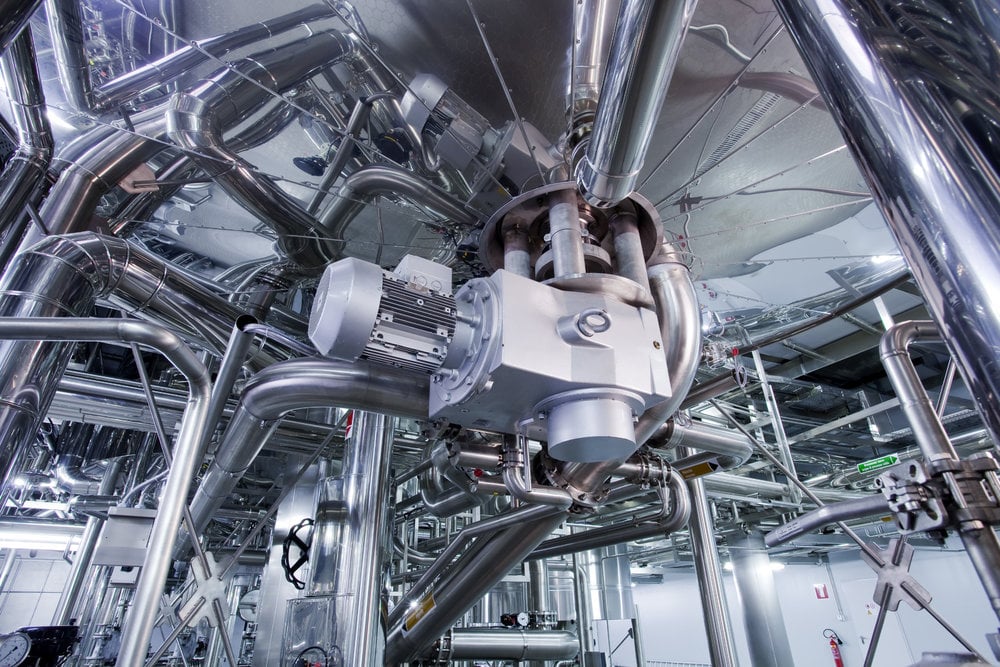
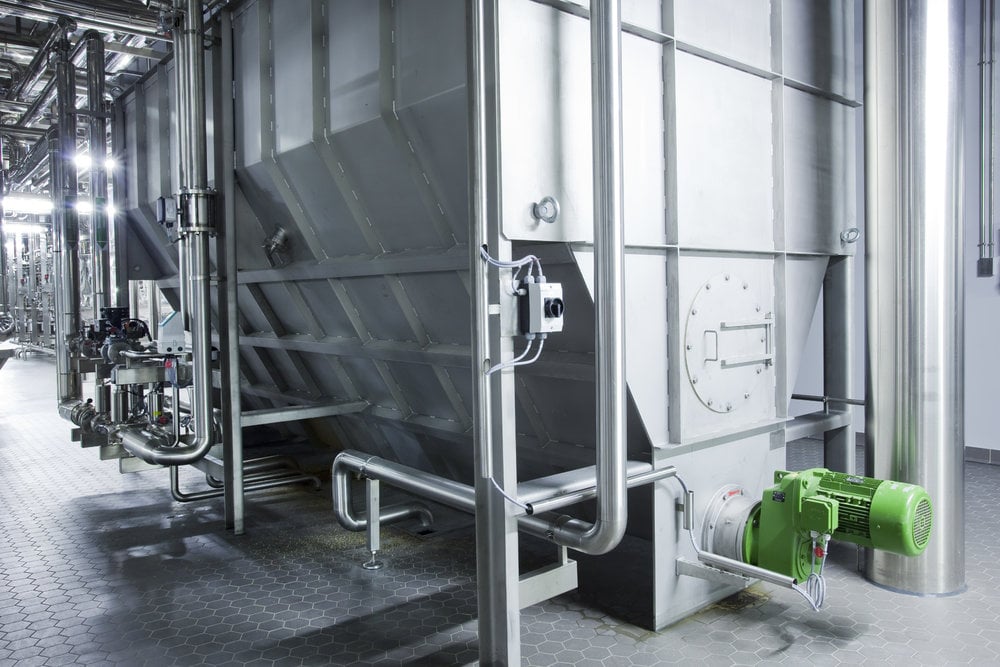
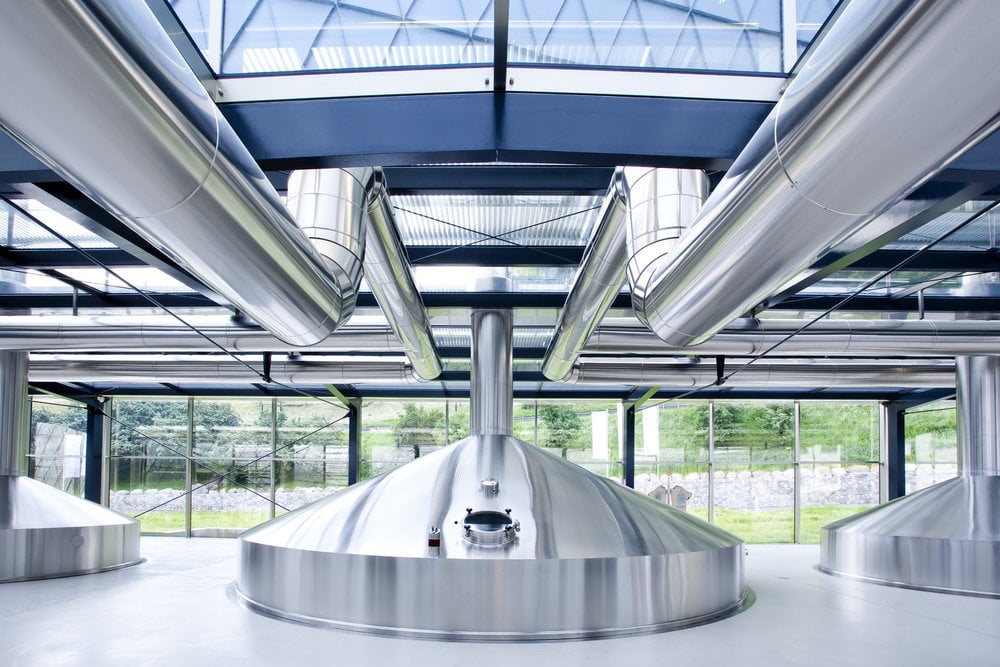
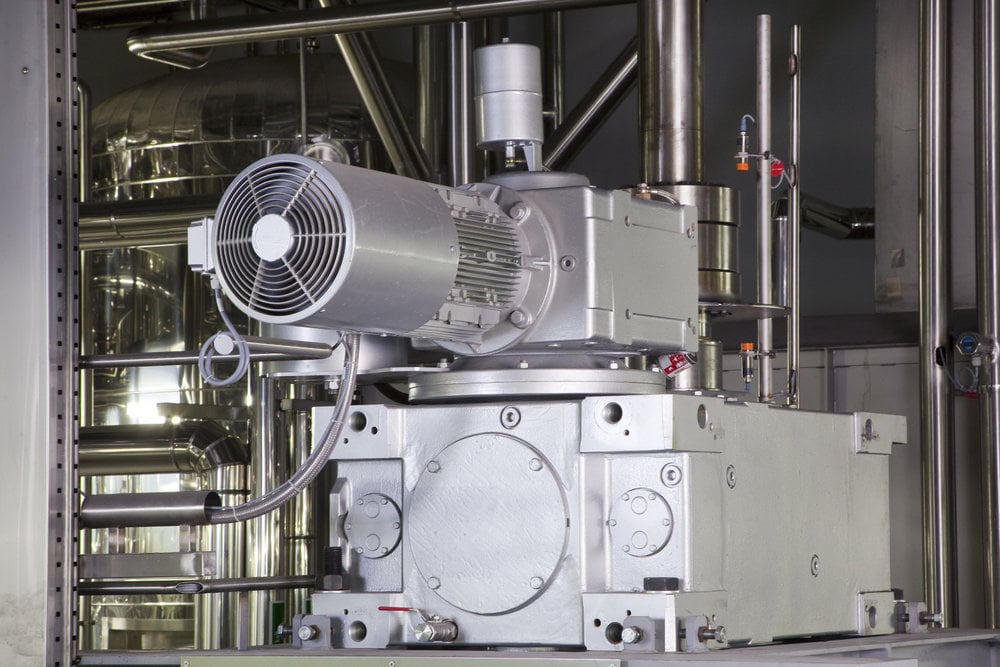
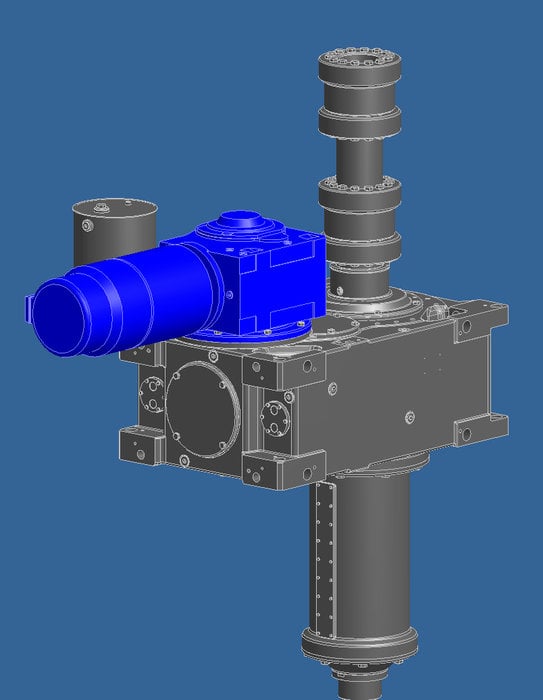
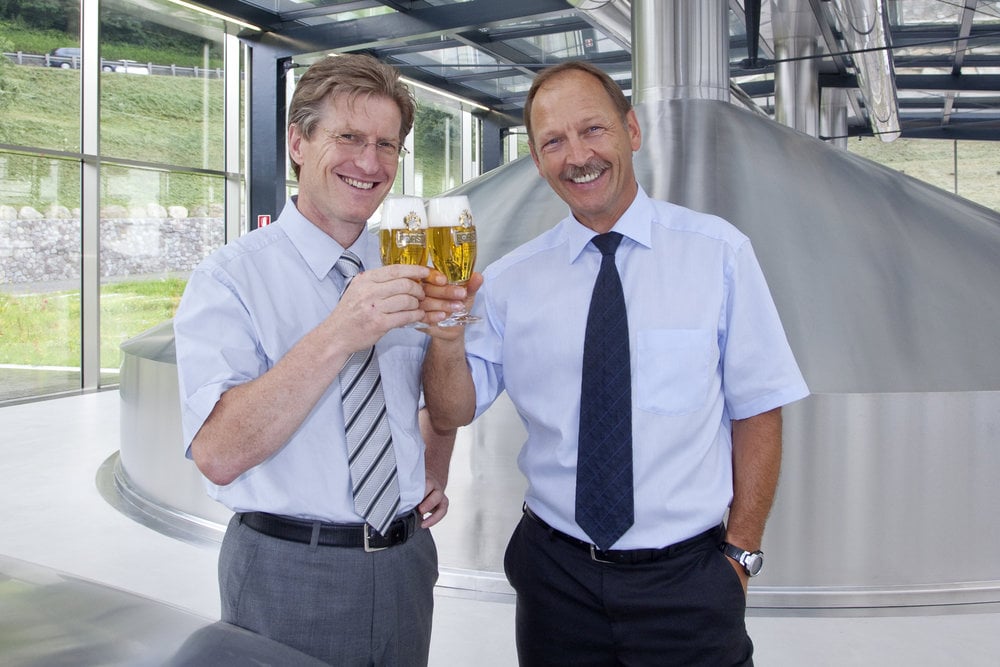