www.industrieweb.fr
19
'20
Written on Modified on
Comment le développement durable s'applique à l'industrie
Les entreprises associent aujourd'hui le terme « durable » aux produits et activités allant de la pêche au mobilier en passant par la consommation d'énergie et l'architecture. L'accent est mis sur la préservation des ressources naturelles et la protection de l'environnement. Cependant, dans un sens plus restreint, l'usinage industriel a toujours suivi une forme de durabilité. L'usinage de produits de haute qualité à des prix compétitifs permet à un fabricant de réaliser des bénéfices et ainsi de maintenir son existence en tant qu'entreprise.
Tout au long de l'histoire, les industriels ont cherché des moyens de rendre leurs procédés d'usinage plus efficaces et plus rentables. Ces efforts consistent en un développement continu de machines de production perfectionnées et précises, l'amélioration des outils coupants et l'optimisation globale des procédés de coupe. Parmi les stratégies plus spécifiques, on trouve l'usinage à grande vitesse, l'usinage grande avance, l'usinage hautes performances et l'usinage numérique.L'initiative récente appelée usinage durable vise à réduire la consommation de matières premières, d'énergie et de la production de déchets tout au long du cycle de vie des produits, à un niveau qui soit au moins en équilibre avec la capacité de régénération de notre planète. Souvent, la discussion générale sur le développement durable se concentre sur les grands problèmes environnementaux mondiaux, mais néglige les éléments de base que sont le prix, le coût, la satisfaction des clients, la connaissance des processus et la fiabilité. Pour ce qui est de la durabilité dans l'usinage, un véritable succès commence par des étapes ainsi que des analyses simples et directes.
Une tarification durable
Chaque entreprise est confrontée au défi de fixer des prix durables pour ses biens ou services. Le prix doit être suffisamment élevé pour couvrir les coûts et générer un bénéfice, mais suffisamment bas pour ne pas pousser les clients à se tourner vers la concurrence. Un industriel peut fixer un prix plus élevé seulement si le client perçoit que le produit apporte une valeur suffisante au regard de ce qu'il paie.
Par ailleurs, si la pression exercée par les clients et les concurrents conduit à fixer un prix trop bas, les marges bénéficiaires en pâtissent. Lorsque le prix est inférieur au coût de production du produit, des pertes en découlent. Si les pressions concurrentielles poussent le prix trop à la baisse, ceux qui conçoivent et usinent le produit doivent trouver des moyens de le produire moins cher, plus rapidement et plus efficacement pour réduire les coûts de production et soutenir une marge bénéficiaire durable.
Les coûts invisibles
Cependant, dans de nombreuses entreprises, le seuil à partir duquel les coûts cessent et les profits commencent n'est pas clair. Cela est dû au fait que les coûts réels eux-mêmes ne sont pas non plus clairement définis. Des facteurs cachés, ignorés ou inconnus n'entrent pas en compte dans le calcul des coûts. Les coûts invisibles typiques sont par exemple les temps d'arrêt non planifiés, les pièces usinées rejetées et la casse d'outils. Ces coûts ne sont pas considérés comme représentatifs ou « réels ». Le comportement ou état d'esprit qui conduit à l'invisibilité de certains facteurs de coût n'est pas limité au personnel de l'atelier ; il peut se rencontrer dans toute l'entreprise.
Pour parvenir à une structure de coûts durable, il faut rendre l'invisible visible. Le personnel de l'atelier doit examiner et évaluer le procédé d'usinage ainsi que la structure et le flux des activités de l'entreprise dans son ensemble afin de découvrir les coûts cachés.
La satisfaction des clients
La satisfaction des clients est un élément clé de la durabilité économique. Un client souhaite savoir quand sa commande arrivera. Le délai de production, dans l'esprit d'un client, commence lorsqu'il passe commande. Cependant, le délai global de fabrication n'est pas exclusivement le temps de production. Si l'usinage d'une pièce nécessite un délai de trois semaines, mais que les activités administratives prennent finalement deux semaines supplémentaires, l'atelier doit être honnête avec lui-même et avec ses clients en indiquant un délai de cinq semaines. Les fournisseurs de l'industrie de l'usinage, dont Seco Tools, proposent des systèmes de gestion des stocks, d'identification des outils et de surveillance des machines qui permettent aux opérateurs de suivre les commandes des clients. Ils optimisent ainsi la capacité de l'atelier à respecter les délais et à satisfaire les clients. (voir l'encadré)
Déchets et mesures
Une production efficace minimise les pertes de temps, d'énergie et de matières premières. Les problèmes liés aux déchets d'usinage tels que les copeaux, les huiles de coupe et les fluides de refroidissement sont complexes. Les industriels considèrent traditionnellement les déchets comme un résultat inévitable des processus et estiment que le changement est difficile à mettre en œuvre, donc son résultat comme marginal. L'attitude dominante dans l'industrie est de se dire : « c'est comme cela que ça marche, il faut faire avec ».
Pour réduire efficacement les déchets et préserver les ressources, il est nécessaire de bien comprendre les caractéristiques des matières et des procédés d'usinage. La compréhension implique une mesure précise des paramètres et des processus de production afin de déterminer exactement les actions mises en œuvre et les résultats réels. La véritable précision évite l'utilisation de chiffres arrondis ; ceux-ci indiquent généralement une connaissance incomplète du processus en cours et empêchent une analyse valable des résultats, lorsque des changements sont apportés. Si un atelier prétend que l'efficacité de sa production est « supérieure à 60 % », est-ce 61 % ou 95 % ? Les deux sont au-dessus de 60 %. De même, une vitesse de coupe d'« environ 200 m/min » n'est pas une information fiable. En réalité, la vitesse sera probablement soit de 206 m/min ou de 195 m/min.
Pour illustrer ce phénomène, prenons le cas d'un responsable d'atelier qui était convaincu que son usine utilisait 70 % (nombre arrondi) du temps disponible pour l'usinage. Une mesure minutieuse a déterminé qu'en fait ce taux n'était que de 34 %. Pour simplifier, dans son atelier sur trois machines, une seule était opérationnelle et les deux autres inactives. Ainsi, la mesure non rigoureuse du responsable de l'atelier (l'approximation) s'est révélée inutile.
Salaire et durabilité
Si nous analysons la durabilité en corrélation avec les coûts mondiaux de la main-d'œuvre, l'évaluation de la productivité de la main-d'œuvre devrait exclure les coûts salariaux. La productivité de la main-d'œuvre est égale au chiffre d'affaires de la production, moins les coûts des biens et services achetés, divisé par le nombre d'employés, divisé à nouveau par une unité de temps.
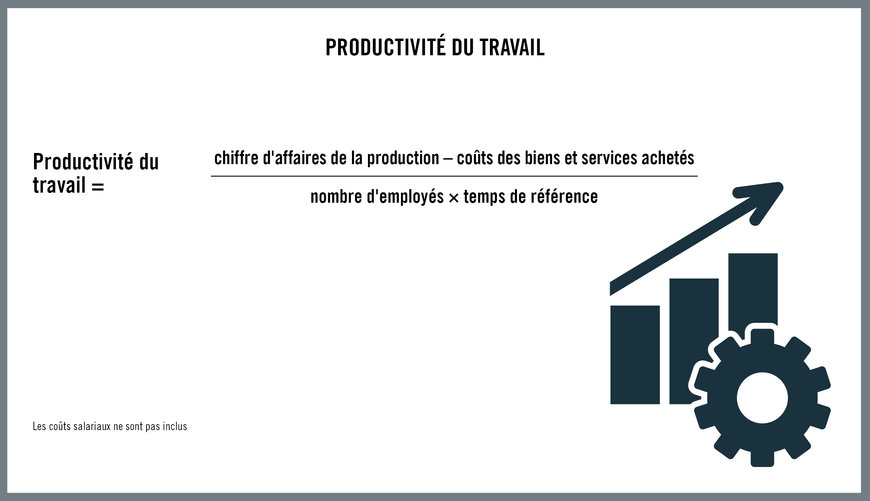
Figure 1:
HQ_ILL_Labor Productivity.jpg
Cette formule mesure la productivité de la main-d'œuvre indépendamment de son coût et permet des comparaisons intéressantes de la productivité de la main-d'œuvre entre des pays ou des entreprises dont les échelles salariales diffèrent. Le salaire d'un opérateur qualifié d'un pays occidental, par exemple, peut être dix fois supérieur à celui de son homologue d'un pays à faible salaire, cette différence ne reflète pourtant pas une productivité réelle. Il est ainsi possible que 10 opérateurs d'un pays à bas salaire produisent moins de pièces, de moindre qualité, qu'un seul opérateur occidental.
Cependant, si la productivité réelle du travail (telle que mesurée ci-dessus) dans le pays à faible salaire est au même niveau qu'en Occident, la recherche d'une productivité économiquement durable dans le pays occidental nécessite des investissements dans des technologies et des méthodes de production innovantes ainsi que la formation continue du personnel.
Une productivité du travail élevée indique que les opérateurs de production ont une compréhension approfondie de ce qu'ils font et qu'ils possèdent de vastes connaissances et compétences. Cela leur permet de travailler plus rapidement, de tirer pleinement profit de leurs compétences et d'augmenter leur satisfaction professionnelle. Les imprévus en usinage sont frustrants pour un opérateur qualifié. Cela se produit fréquemment dans les cas des productions de petites séries diversifiées, où les produits et la taille des lots changent très souvent. Cependant, les opérations peuvent rapidement être ajustées par des opérateurs qualifiés et pluridisciplinaires pour surmonter les goulots d'étranglement et autres événements perturbateurs.
Un processus fiable
Un procédé d'usinage durable doit être fiable, prévisible et minimiser les pertes d'énergie. En effet, un processus peu fiable conduit à la nécessité de re-usiner ou jusqu'à mettre au rebut des pièces. Cela entraîne du gaspillage de matières premières, d'énergie et de main-d'œuvre qui ont été utilisées pour produire le travail rejeté.
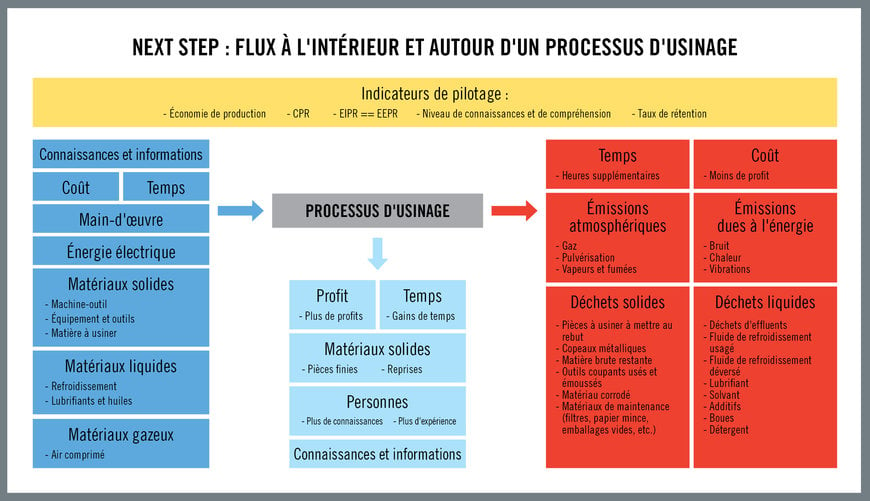
Figure 2:
HQ_ILL_Next Step Streams In And Around A Machining Process.jpg
Dans la même veine, du point de vue du développement durable, le travail en cours (WIP : work in process) se rapporte essentiellement au gaspillage, ce sont des matières ou pièces en attente d'être prises en charge ou d'une opération. D'un point de vue économique, le WIP représente donc une perte d'argent, de temps et de surface de travail. En outre, il est toujours possible qu'une pièce semi-finie stockée soit endommagée lorsqu'elle est déplacée au sein du système logistique. Par conséquent, un atelier doit réduire au maximum son WIP.
Réduction de la consommation d'énergie
Tout au long de l'histoire, l'industrie a trouvé des moyens d'obtenir de meilleurs résultats en utilisant moins d'énergie. Par exemple, au début des années 1980, de nombreux ateliers avaient des machines de 70 kilowatts ou plus. Aujourd'hui, les fraiseuses de 7 kilowatts démontrent une productivité qui peut être supérieure à celle de ces machines dix fois plus puissantes. Un procédé d'usinage durable minimise l'énergie consommée par mm² ou pouce² de matière enlevée. La réduction de la consommation d'énergie entraîne automatiquement une diminution du gaspillage d'énergie, ce qui rend l'usinage plus respectueux de l'environnement.
Maximiser l'efficacité
La figure 3 illustre la consommation d'énergie électrique d'un centre d'usinage 5 axes pendant une journée de travail (ces données ont été recueillies à partir d'une seule machine et constituent une référence générale). Étonnamment, la broche principale ne consomme pas la majorité de l'énergie utilisée par la machine. Les moteurs d'entraînement de l'axe et de la broche principale n'utilisent généralement que 30 % de l'énergie, tandis que les différents systèmes de refroidissement en consomment 44 %, et les pompes, les transformateurs, la commande des machines et d'autres systèmes consomment le reste. Par conséquent, même lorsque la machine ne coupe pas, la plupart des autres systèmes de la machine continuent d'utiliser de l'énergie.
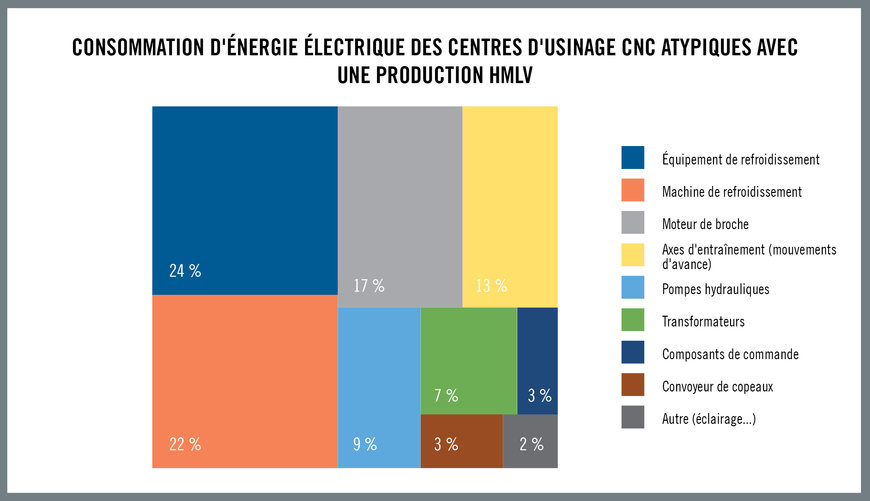
Figure 3:
HQ_ILL_Consumption Of Electrical Energy Of Atypical CNC Milling Machine In HMLV Production.jpg
Une utilisation efficace de l'énergie peut augmenter considérablement le rendement de la production, avec une augmentation minimale de la consommation globale d'énergie. Pour illustrer ceci, prenons comme exemple un premier scenario d'un usinage réel d'une pièce, il prend une heure. Si la programmation, la configuration et le temps d'attente nécessitent six heures, la machine ne va produire que deux pièces par jour et cela en huit heures. Lorsque la machine est en cours de coupe, la consommation d'énergie peut être considérée comme étant de 100 %, ou théoriquement une unité. L'opération de coupe utilise 20 % de l'énergie, donc lorsque la machine ne coupe pas, elle consomme 80 % d'une unité d'énergie. Par conséquent, la consommation totale d'énergie pour la journée est de 6,8 unités tandis que la machine produit deux pièces.
Un deuxième scénario suit l'analyse du processus avec une attention particulière portée à éliminer toute perte de temps. L'analyse permet de réduire le temps d'inactivité à 5 heures, soit une réduction de 16,5 %. Trois heures de temps d'usinage sont désormais possibles, ce qui permet la production de trois pièces. La consommation d'énergie totale par jour est donc de 7 unités, soit 3 % de plus que dans le premier scénario.
La production d'une pièce dans le premier scénario nécessite 3,4 unités d'énergie, tandis que dans le second, la production de chaque pièce nécessite 2,2 unités d'énergie. Dans le deuxième scénario, la consommation d'énergie par pièce diminue de 36 % pour une augmentation de seulement 3 % de la consommation d'énergie quotidienne. La production de trois pièces dans le premier scénario exigerait que la machine fonctionne plus longtemps et consomme plus d'énergie. L'usinage durable ne consiste pas nécessairement à consommer moins d'énergie, mais à usiner davantage avec l'énergie consommée.
Conclusion
Les industriels recherchent depuis longtemps la durabilité économique par l'usinage de produits de haute qualité à des prix compétitifs qui leur permettent de soutenir et de maintenir leurs entreprises. La durabilité économique comprend de nombreuses composantes, mais en général, celles-ci sont simples et fondamentales. La plupart d'entre elles impliquent une évaluation réaliste, honnête et précise puis l'élimination des sources de gaspillage dans toutes les étapes du processus de production.
Pour parvenir à la durabilité économique, les industriels s'attaquent à des problématiques qui leur permettent également de prendre en compte et de réduire l'impact de leurs activités sur l'environnement et de parvenir à un développement durable au sens le plus large du terme.
(Encadré)
Mesures et développement durable
L'organisation et la mesure des facteurs de production et des équipements constituent une étape importante pour l'élimination des déchets et la mise en place de processus d'usinage durables. Pour savoir exactement à quel niveau les pertes de temps et d'énergie se produisent, les opérateurs doivent travailler avec des chiffres et des faits précis plutôt que des spéculations et des estimations basées sur des chiffres arrondis.
Au niveau le plus fondamental, les opérateurs de production doivent savoir quels outils sont disponibles et où ils se trouvent dans l'usine. Quand ces informations ne sont pas disponibles, il faut essayer de deviner, émettre des hypothèses et errer à la recherche des outils. La situation peut être qualifiée de « safari » en atelier, tous savent que les outils sont dans le magasin, mais personne ne sait exactement où.
Seco Tools propose des systèmes d'identification et de gestion des outils destinés à éviter de telles situations. Le système de gestion des stocks Seco, par exemple, est un système de distribution industriel polyvalent de haute qualité qui peut être entièrement connecté en réseau à votre système de production. Après avoir été configuré selon les besoins spécifiques d'un site en matière d'outillage, ce système fournit automatiquement des rapports complets pour suivre l'utilisation d'un outil et détecter les anomalies susceptibles d'indiquer des problèmes.
Il est également essentiel d'identifier correctement les outils lorsqu'ils entrent dans le processus de production. L'identification visuelle et manuelle peut être insuffisante lorsque de nombreux outils similaires sont utilisés. Seco Tools s'est associé à IDEM pour proposer un système d'identification numérique des outils grâce à un système de tags qui utilisent la technologie RFID (identification par radiofréquences) et de lecteurs Bluetooth. Avec l'application Tool Identification, les opérateurs peuvent se connecter immédiatement à une base de données de plus de 900 000 outils, via des systèmes d'exploitation iOS (iPhone, iPad, iPod Touch) comme des Android. Les informations fournies incluent les données complètes des outils et une gestion de leur historique, ainsi que d'autres fonctionnalités telles qu'une plateforme d’échange documentaire collaborative, de communication entre utilisateurs. Les opérateurs peuvent également utiliser cette même technologie de tags pour identifier les outils de mesure et autres produits importants dans l'atelier.
Le machine monitoring en temps réel contribue à la durabilité économique en permettant un suivi continu des procédés d'usinage. D'un point de vue durabilité économique en ce qui concerne la satisfaction client, il permet à toute personne de l'atelier d'indiquer immédiatement à un client où se trouve sa commande dans le processus de production, et permet de préciser la date de livraison.
Pour le Machine Monitoring, Seco Tools s'est associé à MachineMetrics, un fournisseur de solutions d'IIoT (Industrial Internet of Things ou Internet des Objets). MachineMetrics se connecte facilement aux Automates Programmables Industriels (API) et au contrôleur de la machine en passant par l’Ethernet, le Wifi ou le réseau cellulaire 4G. Les entrées/sorties numériques et analogiques sont configurées et gérées par une interface web. Basé sur le cloud, le système est facile d'utilisation, entièrement personnalisable et rapide à installer. Il enregistre et fournit des analyses approfondies des données qu’il collecte. Ces données et tableaux de bord fournissent aux utilisateurs les informations nécessaires pour mieux comprendre et optimiser leurs opérations d’usinage, augmenter la disponibilité des machines et libérer de la capacité. Le système permet également d’accéder à la base de données d’outils coupants et de bénéficier de l'expérience Seco, afin que les utilisateurs puissent améliorer leurs processus et utiliser pleinement les données pour mieux optimiser la durée de vie de l’outil, la vitesse de coupe, l’avance ou encore réduire la casse outil.
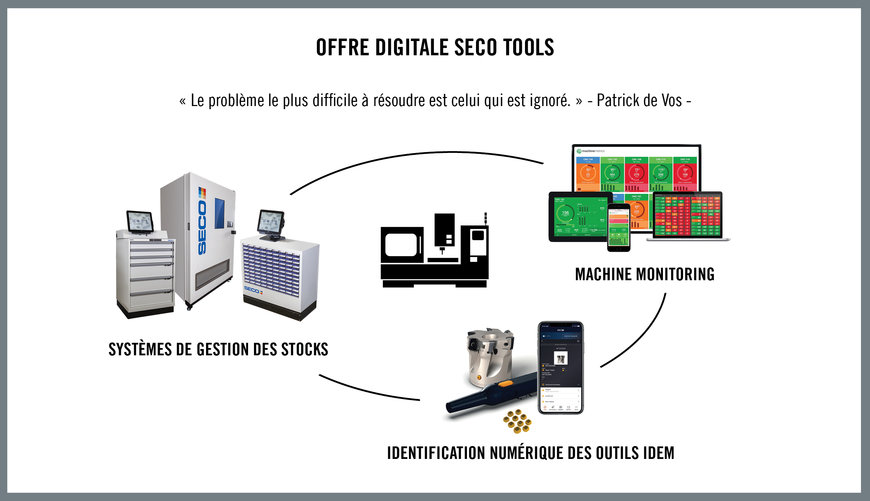
Figure 4:
HQ_ILL_Seco Tools Digital Offering.jpg
Par :
Patrick de Vos, Directeur du développement commercial et Responsable de l'enseignement technique, Seco Consultancy